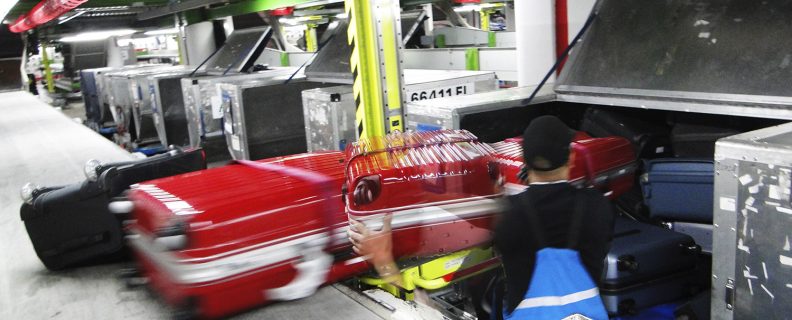
Baggage handling Systems
Leading global provider with extensive experience
Lifts All is a leading global provider of baggage handling systems (BHS). From major to minor airports, our lifting solutions have moved countless bags and saved many backs from injury. Our ground handling equipment makes the work easy, ergonomic, and streamlined.
Equipment for all types of baggage
Hardside suitcases, soft bags, backpacks, and special baggage – we have a lifting solution for almost all types of baggage. Read more about our different solutions below.
Baggage handling systems for airports
Lifts All offers several types of baggage handling systems for airports:
Electric Container Loading System (e-CLS)
Our Container Loading Systems (e-CLS) is for loading bags into containers by means of a telescopic table. Baggage is rolled quickly on and off the e-CLS, either vertically or horizontally, and loading is completed in a flash. The container will be fully loaded in no time. The Container Loading System is suitable for both left and right-handed operators, and can be customized for laterals on the left or the right side.
Electric Container Unloading System (e-CUS)
Our high-capacity Container Unloading System (e-CUS) enables baggage handlers to unload bags effortlessly. Thanks to the slightly tilted tray, baggage slides out of the container and onto the conveyor belt in just seconds.
Technical Credibility
Safety
- EN ISO 12100:2010 Machinery Safety – General Principles for Design – Risk Assessment and Risk Reduction
- SS-EN 13155:2021 Cranes – Safety – Non-fixed lifting accessories
- SIS-ISO/TR 14121-2:2012 Machinery Safety – Risk Assessment – Part 2: Practical Guidance and Examples of Methods
Performance
With this unit, it is possible to unload 20 bags per minute, based on several hours of test cycles.
Installation Timeline
The unit is usually delivered with a rail system. The installation of both the unit and the rail system takes between 12 to 72 hours, depending on the complexity and size of the system.
Product Specifications
Technical Specifications:
-
- Load capacity: 40kg maximum
- Reach: Flexible length 800 mm to 1200 mm
- Power: 400 V AC, 16-hour continuous operation
- Safety features: Emergency stop, overload protection
- Compatibility: All standard ULD containers
Power Requirements:
- Voltage: 400 V AC
- Average consumption: 3.36 kWh/day (24 hours of operation)
Safety Features
Emergency stops:
- 2 emergency buttons placed on the right and left side of pillars, (stop category 0)
Overload protection:
-
- Type: Bi-metallic thermal protection switch (integrated)
- Threshold: Approx. 120–140°C winding temperature
- Response time: Dependent on thermal rise; typically within seconds to minutes under overload conditions
- Compliance: Built-in protection per IEC motor standards (e.g., IEC 60034)
Fail-safes:
Emergency stop (E-stop):
-
-
- Immediate deactivation of all motion and electrical power upon activation.
- Wired to disconnect the power supply directly.
- Complies with EN ISO 13850, Stop Category 0.
-
Thermal overload protection (motor):
-
-
- Integrated bi-metal switch inside Interroll DM0080 drum motor.
- Cuts power if motor winding exceeds approx. 120–140°C.
- Automatic protection against overheating and prolonged overcurrent.
-
Manual reset after E-stop:
-
-
- System requires manual reset after E-stop engagement to avoid unintentional restart.
-
Short-circuit and fuse protection:
-
-
- Circuit breakers or fuses installed on the main supply and control circuits.
-
Performance Metrics / Efficiency Metrics
Time savings: 50% vs manual loading
By reducing the workforce from 2 operators to just 1, the time spent on unloading is significantly reduced. Based on this change, we estimate a time savings of
- Labor reduction: 1 FTE per shift
- Error rate reduction: 80%
Gentler handling reduces the risk of damage to baggage caused by manual throwing onto the carousel. The machine uses a conveyor-like mechanism for smoother and safer delivery.
Installation Process
Phase 1: Pre-Installation
- Site Survey: An inspection is carried out to ensure that the installation site is suitable for the machine.
- Power Requirement Verification: Verification that the power supply is compatible with the machine’s requirements.
- Safety Assessment: A safety review to identify and minimize potential risks.
Phase 2: Installation (Days 1)
- Equipment Mounting: The machine is mounted and placed at the predetermined installation site, and all components are put into place.
- Power Connection: Electrical connections are made to link the machine to the power supply and ensure correct operation.
- Safety System Integration: The safety systems are integrated and tested to ensure that all safety measures work correctly.
Phase 3: Testing (Day 2)
- Load Testing: A load test is performed to ensure that the machine can handle the expected loads without issues.
- Safety System Verification: All safety systems are verified to confirm they meet applicable safety standards.
- Operator Training: Operators are trained in the machine’s functions, safety protocols, and best practices
e-CLS Launcher
Instead of pushing or lifting bags off the tray by hand, the e-CLS Launcher does this for you. Just load the bags onto the tray, press two buttons and the Launcher will push the bags into the container.
Technical Credibility
Safety
- EN ISO 12100:2010 Machinery Safety – General Principles for Design – Risk Assessment and Risk Reduction
- SS-EN 13155:2021 Cranes – Safety – Non-fixed lifting accessories
- SIS-ISO/TR 14121-2:2012 Machinery Safety – Risk Assessment – Part 2: Practical Guidance and Examples of Methods
Performance
With this unit, it is possible to load 10 bags per minute, based on several hours of test cycles.
Installation Timeline
The unit is usually delivered with a rail system. The installation of both the unit and the rail system takes between 12 to 72 hours, depending on the complexity and size of the system.
Product Specifications
Technical Specifications:
- Load capacity: 50kg maximum
- Reach: Max reach 2670 mm
- Power: 220 V AC, 16-hour continuous operation
- Safety features: Emergency stop, overload protection
- Compatibility: All standard ULD containers
Power Requirements:
- Voltage: 220 V AC
Safety Features
Emergency stops:
- 1 emergency buttons placed on the pillar (stop category 0)
Overload protection:
- Compliance: Built-in protection per IEC motor standards (e.g., IEC 60034)
Fail-safes:
Emergency stop (E-stop):
-
-
- Immediate deactivation of all motion and electrical power upon activation.
- Wired to disconnect the power supply directly.
- Complies with EN ISO 13850, Stop Category 0.
-
Manual reset after E-stop:
-
-
- System requires manual reset after E-stop engagement to avoid unintentional restart.
-
Short-circuit and fuse protection:
-
-
- Circuit breakers or fuses installed on the main supply and control circuits.
-
Performance Metrics / Efficiency Metrics
Time savings: 40 % vs manual loading
By significantly reducing the workload for the operator. The baggage handler can work with good speed during the entire shift. Based on this change, we estimate a time savings of 40 %.
- Error rate reduction: 80%
Gentler handling reduces the risk of damage to baggage caused by manual throwing into the ULD. The machine uses a table with omni wheel mechanism for smoother and safer delivery. - Everyone can load bags
- since loading bags is now an easier job, the selection of staff is broader. This means that even physically weaker and older workers can load bags.
Installation Process
Phase 1: Pre-Installation
- Site Survey: An inspection is carried out to ensure that the installation site is suitable for the machine.
- Power Requirement Verification: Verification that the power supply is compatible with the machine’s requirements.
- Safety Assessment: A safety review to identify and minimize potential risks.
Phase 2: Installation (Days 1)
- Equipment Mounting: The machine is mounted and placed at the predetermined installation site, and all components are put into place.
- Power Connection: Electrical connections are made to link the machine to the power supply and ensure correct operation.
- Safety System Integration: The safety systems are integrated and tested to ensure that all safety measures work correctly.
Phase 3: Testing (Day 2)
- Load Testing: A load test is performed to ensure that the machine can handle the expected loads without issues.
- Safety System Verification: All safety systems are verified to confirm they meet applicable safety standards.
- Operator Training: Operators are trained in the machine’s functions, safety protocols, and best practices
Basic Vacuum Gripper
The Basic is a multi-gripper that makes lifting different types of baggage easy. It can lift either by latching onto the bag with a vacuum suction cup, or by picking it up with the integrated hook. The Basic has several smart functions, some of which are, a 360° rotation for precise placement, non-bulky appearance, easy to handle, and an ergonomic handle made for both left and right-handed operators.
SPEED Loader
The SPEED Loader makes unloading baggage from leaning baggage carousels effortless. Just slide to transfer the baggage from the carousel to a conveyor belt or into a ULD container. The extended arm has an excellent range that allows it to reach all the way back into the container.
Effective and safe baggage handling
Lifting baggage manually is a heavy and straining job. Often, it results in slower operation and a decrease in productivity as the baggage handler tires during their work shift. Using a lifting tool will help improve the workflow. By using Lifts All’s baggage handling systems, the strain is taken off the baggage handler. Some users testify to an increase in productivity while others have noticed more consistent energy throughout the day.
Lifts All’s baggage lifting tools are safe to use. Equipped with safety functions, such as emergency stop buttons and load guards, our tools are designed to fulfill the safety standards that will keep baggage handlers protected.
Lifting baggage safely
Millions of bags travel daily from check-in areas to the airport terminals and onwards to airplanes at airports across the world. Baggage handlers are often under intense physical pressure as bags need to move quickly so that they arrive on time. Manually lifting baggage, mail sacks and cargo in and out of containers can be physically harmful. Strain injuries are not uncommon. Using lifting tools, on the other hand, often result in improved ergonomics and increased safety for the baggage handler.
Smooth installation
Lifts All’s baggage handling solutions are installed into the baggage handling areas at airports. Instead of rebuilding or partitioning off new areas to fit the new system, we integrate our system into the preexisting one in the area/baggage hall. The installation process is fuss-free and operation is up and running in no time.
The baggage handling process
Plain sailing airport operations include well-organized airside and landside operations. The baggage throughput rate is a pivotal factor in meeting tight airport schedules. Baggage handling systems are integral for ensuring that bags travel at the right speed to arrive at the same time as their owners. Lifts All’s high-capacity baggage handling systems can be placed at all baggage-intensive points in an airport – at the check-in area, beside transport carts, at the departure gate, at conveyor lines, between gates during transfers, and from the arrival gates to the baggage-claim area. Our lifting solutions help streamline the baggage handling process all the way through the airport.
Each airport has its own baggage handling system. Some airports opt for automated baggage handling systems, and some handle their baggage manually. Manually handling baggage means that the ground handling staff have to lift bags in and out of the aircraft, to and from conveyor belts, and into and off carts and containers, by hand. However, manually handling baggage does not have to be physically strenuous. Baggage lifting equipment is not only ergonomically beneficial, but helps baggage handlers keep up to speed and maintain precision while working.
When and where is a baggage lifting aid suitable?
A baggage lifting aid is often preferred by ground handling companies when baggage is loaded manually. The lifting aid can be installed next to the conveyor belt in the check-in area, next to the baggage carousels, at the final sorting area, or even integrated into baggage screening areas.
As automated baggage handling systems tend to be cumbersome to install, perhaps requiring a rebuild of the facility, a Lifts All baggage lifting aid is much more flexible as it is easily integrated into the current facility. No renovation or reconfiguring of the facility is required. The installation is quick, and the payoff is instantaneous, with increased efficiency and improved ergonomics.